This is my second post in a series of blogs around modular systems and configurable product platforms. In the first post, What makes a Good Modular system? I looked at how good modular systems balance the scope of the systems and their lifespan with the effort to create them.
In this post, I will move beyond the idea of good, balanced module systems into how they can be leveraged transversally across multiple product families to generate even greater profitability. I will continue with the same example company who started with independent module systems and transitioned to ones that are broadly shared.
What is a Modular System?
A modular system is a collection of building blocks that can be configured in different ways, adapting for different customer needs. Over time, some modules will be developed to serve new purposes or to improve performance in some aspect. Optimization and cost-cutting can be done within modules without the typical ripple effect throughout the product and, when done well, without reducing the value to customers. Many companies use modularization and configurable product platforms as tools to reduce product complexity or to make the customer order process more efficient by configuring-to-order rather than engineering-to-order.
If you are interested to know how a Modular design differs from traditional design you should read this blog Accelerate Agility, Flexibility and Efficiency with Modular Design
The most obvious and traditionally known way to create modular systems is to group a number of product families that share technical properties (technology and sizing) and supply chain properties (factory footprint and supplier base) into a shared platform. The system, in this case, is scoped as end-to-end products. Functions that exist across other product families are typically not evaluated as such which limits possible transversal sharing.
This inevitably leads to sub-optimization where functions are customized and re-evaluated towards the specific platform, rather than optimized from a holistic point of view. In the worst case, the customizations are not necessary from a performance perspective and may even decrease customer value. In all cases, they become a barrier for supply chain and aftermarket efficiency improvements that would benefit from greater commonality.
High-Level Modular Systems and Shared Modular Systems
Some leading companies have taken it to the next level by defining a wide-scope modular system, also called a unified product platform. This is a system of modular systems that can be shared across multiple products. The modular system may include multiple product architectures, enabling massive benefits for scale and flexibility, and reduced cost of complexity.
One example of such a leading company is Volkswagen Group (VW), the world’s largest auto manufacturer. VW has consistently pushed the boundaries of product platforms and architecture, marking the direction of the whole industry. I often use them as an example of all sorts of benefits connected to modular systems. In this blog post I will use VW to explain the concept of high-level shared modular systems and unified product platforms.
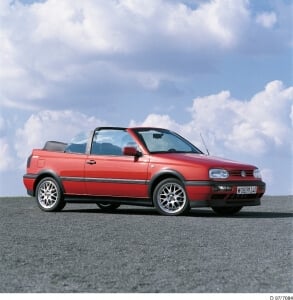
In the early 1990’s VW pioneered the use of shared platforms in the auto industry. VW had acquired AUDI in the mid 1960’s, SEAT in 1986 and SKODA in 1991 and was manufacturing more than 20 different car models. By sharing a standardized base frame between multiple models and brands, economies of scale could be reached for component such as drivelines, interiors and chassis. Over time, the approach was criticized for limiting the ability to adapt the product to different brand images. This hurts the status of premium brands, but also increases the risk of not reaching low enough cost levels for value brands.
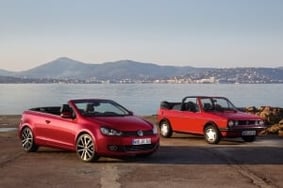
The second generation of VW’s platform concept came in the mid 2000’s. There is a clear switch from standardization to modularization, enabling wider platforms with increased economies of scale. All Audi production cars were now being built from the same platform – a dream for the supply chain. They enabled huge increases in efficiency, fewer assembly lines and greater purchasing leverage.
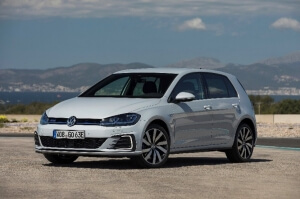
One decade later, mid 2010’s, the bomb dropped, and it is called MQB (german for Modularer Quer Baukasten, roughly translated as Modular Transversal Engine Building System). VW was now aiming to build cars of practically any size from the same product platform. In the end of 2020, the MQB platform encompasses more than 80% of the VW production volume. Since then, the focus has shifted towards BEV platforms, and the targets have been set even higher. By 2025 VW group is planning to supply all their passenger cars from a single unified platform, the SSP.
A Modular System Does not have to Span a Product End-to-End
I will use Volkswagen to explain what a product architecture is, what a modular system is and how modules relate to both concepts. As already mentioned, I define a high-level modular system, as a system of modular subsystems that is configured on all levels. Here, I illustrate it in relation to an end-to-end-product, showing that each modular system spans only a portion of the full product:
To date, VW has a number of (Modulare Baukästen or Modular Building Systems.) They have MQB, as already mentioned, but also MLB for longitudinal engines and MMB for mid-engine cars. For electric drivelines, we have the MEB and PPE platforms. In actuality, these additional platforms only exist because VW has many premium, high-performance cars in their portfolio, especially under the Porsche and Audi brands.
As mentioned earlier, the bulk of VW’s volume today is covered by MQB. What is especially interesting to note is that this platform and all of the others are instances of the same high-level modular system. What I mean is that the different platforms can include shared transversal subsystems, and this is what is happening when VW is merging their three BEV platforms into one, the SSP platform. To explain this concept, I will use the electric MEB platform:
The MEB is VW group’s first all-electric platform, built completely around the electric drivetrain. Obviously, one of the most important parts of any battery-powered electric platform is the battery. And here comes the point… the battery is actually a modular system of its own. A modular system that could be designed to be shared with the other electric platforms, including the PPE for premium high-performance electric cars.
The important factors for configuring a battery are how much space you have at hand and how much energy you need to store. If the different platforms can share the same high-voltage interface and battery footprint logic, there is no reason why this modular system could not be shared.
This is a modular system that can be configured to deliver different levels of battery capacity, charging performance and be adapted to the available footprint. Many of the modules inside the system can be standardized for an enormous volume consolidation. This includes, for example, the cell module, cell management controller and high voltage connector. It creates huge benefit when setting up the new battery supply chain. VW even sell their electric platform to other car makers, further expanding the consolidated volumes and making the investments in development and supply chain even more profitable.
Shared Modular Systems
To add clarity, let me put some words from the VW Electric car platforms on the boxes in the earlier high-level modular system illustration to show how these platforms are evolving into SSP. This is only illustrative, not facts:
Finally, you see modularity on different levels and an extremely systematic approach that can be leveraged across the functions of the company, e.g. Production, Strategic Product Planning, and Sales.
Product Architecture and Shared Modular Systems in other Industries
The very same thinking can be applied in many other product segments in both industrial and consumer goods: appliances, machinery, equipment, etc.
For example, in the home appliance industry the tradition is to see different types of appliances as different platforms. They would say that there is one (or many) platform for washing machines and another platform for dryers. While this makes sense from a functional perspective, it lacks the perspective of industrial design and production.
Shared Styling and User Interface Across Product Types
Since the washers and dryers are typically used in combination and located together in our homes, you clearly want them to have a common design for both the aesthetics and the user interface. From a modular system standpoint, it makes a lot more sense to see the front panel and user interface as a shared transversal product platform rather than parts that must be aligned across the washer and dryer modular systems. This way, you can introduce updates to both the styling and user interface simultaneously across the two product lines. This also matches the expectations for customers who are looking for consistency in the look and operation.
Flexible Line Assembly
A driving factor in the home appliance industry, just as in the car industry, is to produce many products on the same flexible assembly lines while keeping them efficient. An enabler for this is the harmonization of the approach to structural design, enabling the use of the same tools, assembly order, etc.
Let’s say that you want to produce washers and dryers on the same assembly line. This would be a clear motivation to include them in the same product architecture, sharing as many of the underlying module systems and interfaces between them as possible.
Using the same way of illustrating the product architecture for washers and dryers:
A shared system for control and communication could also be used across other home appliance products, including hardware and software for IoT, controls, etc.
Final Words
In this blog post I have defined a high-level modular system as a system of modular systems that is configured on all levels. To me, this is one of the most important realizations a company must have to enable the shift towards further increased alignment between strategy, organization, and product, and reach further on their modular way. In my previous post, What makes a Good Modular System, I have suggested a schematic model to understand how to scope profitable modular systems. For more information, feel free to download your 5-step guide on how to create a modular Product Architecture below.
AUTHOR
Tobias Martin
Vice President & Partner
+46 8 456 35 00
tobias.martin@modularmanagement.com
Volkswagen pictures courtesy of Volkswagen Group AG.